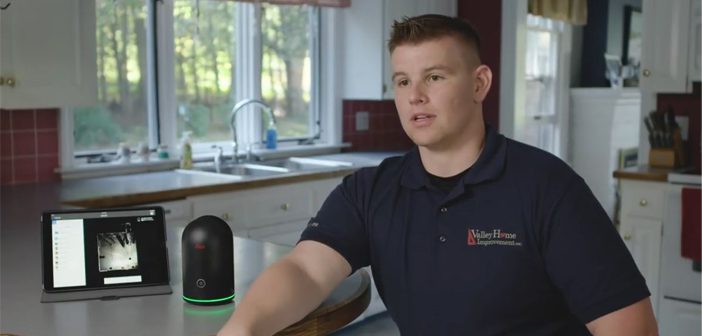
Leica BLK360 International Series #2: 3 ways Leica BLK360 improved workflow
Stephen Gross, an Architectural Engineer at Valley Home Improvement in Northampton, Massachusetts, has had his Leica BLK360 since August of 2017. He recently shared with us how using the BLK360 has improved his workflow.
#1: Site Visit Changes
Before the Leica BLK360, you would walk into a space with an idea of the items and information you need to get. This information is project dependent, of course, but includes everything from specific plumbing locations, wall thickness, door and window sizes and locations, ceiling heights, and on and on. At the time, we used to have to try to transition real-world 3D as-built data into a 2D drawing on paper, then back to 3D data again in design software. But there is only so much data you can fit on a few sheets of graph paper, and only so much time you can invade the home or business of a potential client.
It begs the question, “Can we find a way to skip the step of the “2D” copy of site data, and just take the property with us and reference it on our schedule?” The answer is yes. By helping us take entire scans with us back to the office, it made us more accurate, more efficient, and way less stressed.
#2: Working With Precision Data
Working in renovations, we’ve run into several occasions where having the Leica BLK360 has saved us a lot of time (and gas). Because we had our scans, we didn’t have to go back out to check when a dimension or other existing condition didn’t quite add up. This was especially true for a recent project. Dealing with projects ranging from colonial America to modern construction has its curve balls, specifically with analysing an existing roof structure.
A current project has a roof with 2×8’s flat roof span and limited access for reinforcing. It’s presented us with an interesting engineering problem. The scan data has helped us out tremendously. For one, it has allowed us to understand that reinforcing in such a small accessible space will not be cost-effective.
It also has allowed us to design and construct a steel frame bridging the exterior support walls, and avoid major upgrades to the existing structure. Working with true data has been a huge time-saver.
#3: Progressive Scan Data
With any renovation, plans are subject to change as soon as the walls are opened up. On a lot of our larger projects, we will take progressive scans to record rough plumbing, electrical, and other conditions before all the finishes are up. Because our company offers a warranty program, in the rare event of an issue, we can use this information to help diagnose the culprit and locate and plan access points that mitigate the amount of demo we have to do to contain the issue. In those cases, having progressive scans is crucial.
Stephen Gross, Architectural Engineer for Valley Home Improvement, took us out in the field for a site survey and filled us in on the efficiencies they’ve gained by making reality capture a part of their work.
WATCH: Leica BLK360 Improved Workflow
Is the Leica BLK360 the right solution for you?
Contact us on 0800 453 422 or info@globalsurvey.co.nz
SHARE THIS ARTICLE